Motosiklet Kasklarının Dış Kabuk Yapıları ve Üretim Süreçleri
02-01-2024
14:53
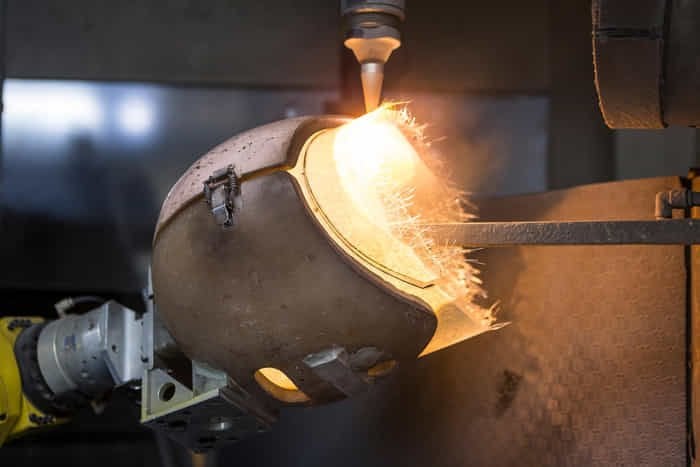
Motosiklet Kaskların Dış Kabukları ve Üretim Süreçleri
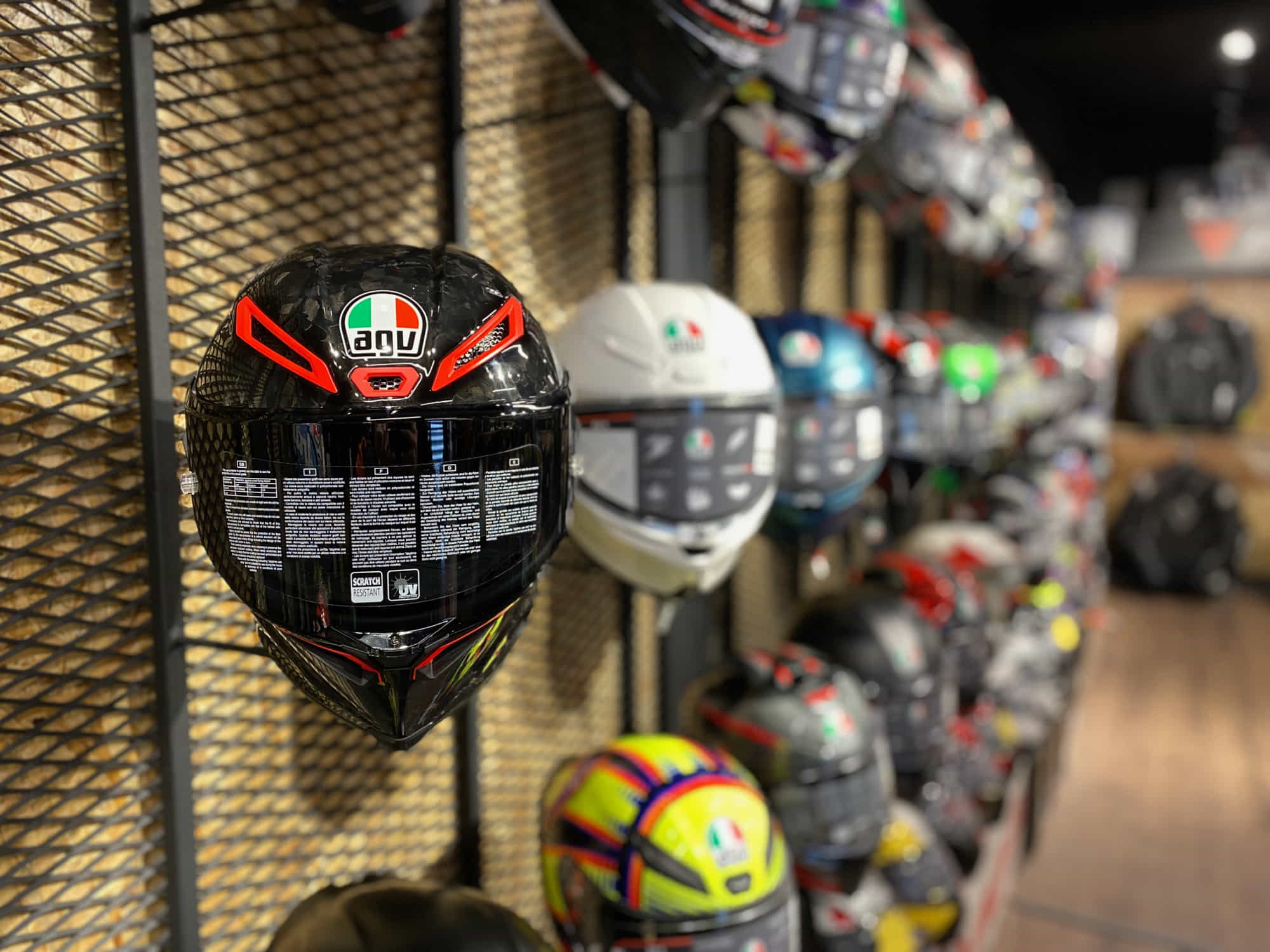
Motosiklet kaskları, sürücülerin güvenliği açısından kritik öneme sahip olan koruyucu ekipmanlardır. Bu kaskların dış kabukları, genellikle farklı malzemeler ve üretim süreçleri kullanılarak şekillendirilir. Bu blog yazısında, motosiklet kasklarının dış kabuk yapılarına ve üretim süreçlerine odaklanacağız.
1. Polikarbon Dış Kabuklar
Polikarbon, ekonomik ve hafif bir malzeme olarak bilinir. Genellikle giriş seviyesi kask modellerinde tercih edilir. Polikarbon dış kabuklar, darbeye karşı direnç sağlar ve kullanıcılara uygun fiyatlı bir güvenlik seçeneği sunar.
2. Fiberglass Dış Kabuklar
Orta seviye ve yüksek performanslı kasklarda sıkça kullanılan fiberglass, dayanıklılık ve mukavemet sağlayan bir malzemedir. Fiberglass dış kabuklar, genellikle hafif olmaları ve çeşitli tasarım detaylarına imkan tanımaları nedeniyle tercih edilir.
3. Karbon Fiber Dış Kabuklar
Yüksek performans ve premium kask modellerinde sıklıkla gördüğümüz karbon fiber, mükemmel mukavemeti ve hafifliğiyle öne çıkar. Karbon fiber dış kabuklar, genellikle motorsporları ve performans odaklı sürüşler için tercih edilir, ancak genellikle daha yüksek maliyetlidir.
4. ABS (Akrilonitril Bütadien Stiren) Dış Kabuklar
ABS, ekonomik ve darbeye karşı dirençli bir termoplastik malzemedir. Bu malzeme, genellikle giriş seviyesi kask modellerinde kullanılır. ABS dış kabuklar, hafiflik ve uygun maliyet avantajları sunar.
5. Kompozit Dış Kabuklar
Kompozit dış kabuklar, genellikle fiberglass, karbon fiber ve aramid (örneğin, kevlar) gibi farklı malzemelerin birleşimini içerir. Bu kombinasyonlar, mükemmel mukavemet, hafiflik ve darbe direnci sağlar. Kompozit dış kabuklar, orta seviye ve üst seviye kasklarda yaygın olarak bulunur.
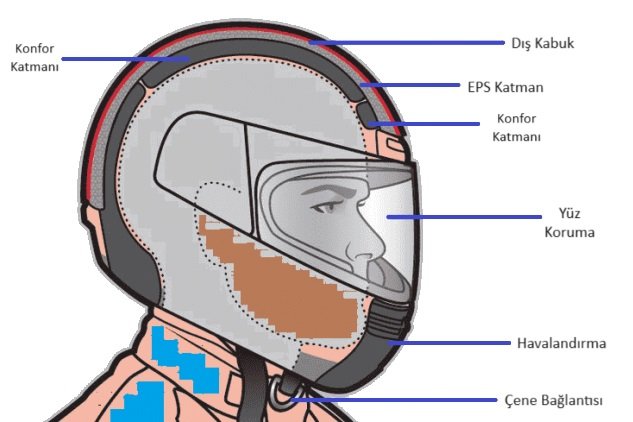
Motosiklet Kaskların Dış Kabuk Yapısının Üretim Süreci
Her dış kabuk malzemesi için özel bir üretim süreci bulunmaktadır. Ancak genel olarak, üretim aşamaları şu adımları içerir:
1. Malzeme Seçimi:
Üretim süreci, kaskın kullanım amacına uygun malzemenin seçimiyle başlar. Polikarbon, fiberglass, karbon fiber veya diğer kompozit malzemeler arasından bir tercih yapılır.
2. Kalıp Hazırlığı:
Tasarım özelliklerine uygun kalıplar hazırlanır. Bu kalıplar, kaskın dış kabuğunun istenilen şeklini almasını sağlar.
3. Malzeme Hazırlığı:
Seçilen malzeme, üretim süreci için hazırlanır. Polikarbon gibi termoplastik malzemeler enjeksiyon kalıplama için eritilirken, fiberglass ve karbon fiber gibi malzemeler önceden belirlenmiş desenlere göre kesilir.
4. Enjeksiyon veya Kalıp İşleme:
Polikarbon: Eritilmiş polikarbon malzemesi, enjeksiyon işlemi ile kalıba enjekte edilir.
Fiberglass ve Karbon Fiber: Kesilmiş malzeme, önceden hazırlanmış kalıplar içine yerleştirilir ve şekillendirilir.
5. Sıkıştırma ve Sertleşme:
Polikarbon: Enjekte edilen malzeme, belirli bir sıcaklık ve basınçta sıkıştırılır.
Fiberglass ve Karbon Fiber: Malzeme sertleşme sürecine geçer ve belirli bir basınç altında şekillenir.
6. Pişirme (Kürleşme):
Kaskın dış kabuğu, belirli bir sıcaklıkta fırınlanarak (kürleştirilerek) malzemenin tamamen sertleşmesi sağlanır.
7. Kalıp İşleme:
Sertleşen dış kabuk, kalıplar yardımıyla şekillendirilir. Bu aşamada, kaskın tasarımı ve detayları belirlenir.
8. Montaj:
Dış kabuk, kaskın diğer bileşenleri ile birleştirilir. Vizör, iç pedler, kemer sistemi ve diğer parçalar eklenir.
9. Kalite Kontrol:
Üretim sürecinin her aşamasında kalite kontrol uygulanır. Kaskın dış kabuğu ve montajı dikkatlice incelenir, güvenlik standartlarına uygunluğu sağlanır.
10. Testler ve Onaylar:
Üretilen kasklar, çeşitli testlere tabi tutularak güvenlik standartlarına uygunluğu sağlanır. Darbe testleri, penetrasyon testleri ve diğer güvenlik kontrolleri yapılır.
Bu detaylandırılmış süreç, farklı malzemelerin kullanıldığı ve farklı teknolojilerin uygulandığı üretim aşamalarını yansıtmaktadır. Her adım, kaskın maksimum dayanıklılığını, güvenliğini ve performansını sağlamak amacıyla özenle yönetilir.
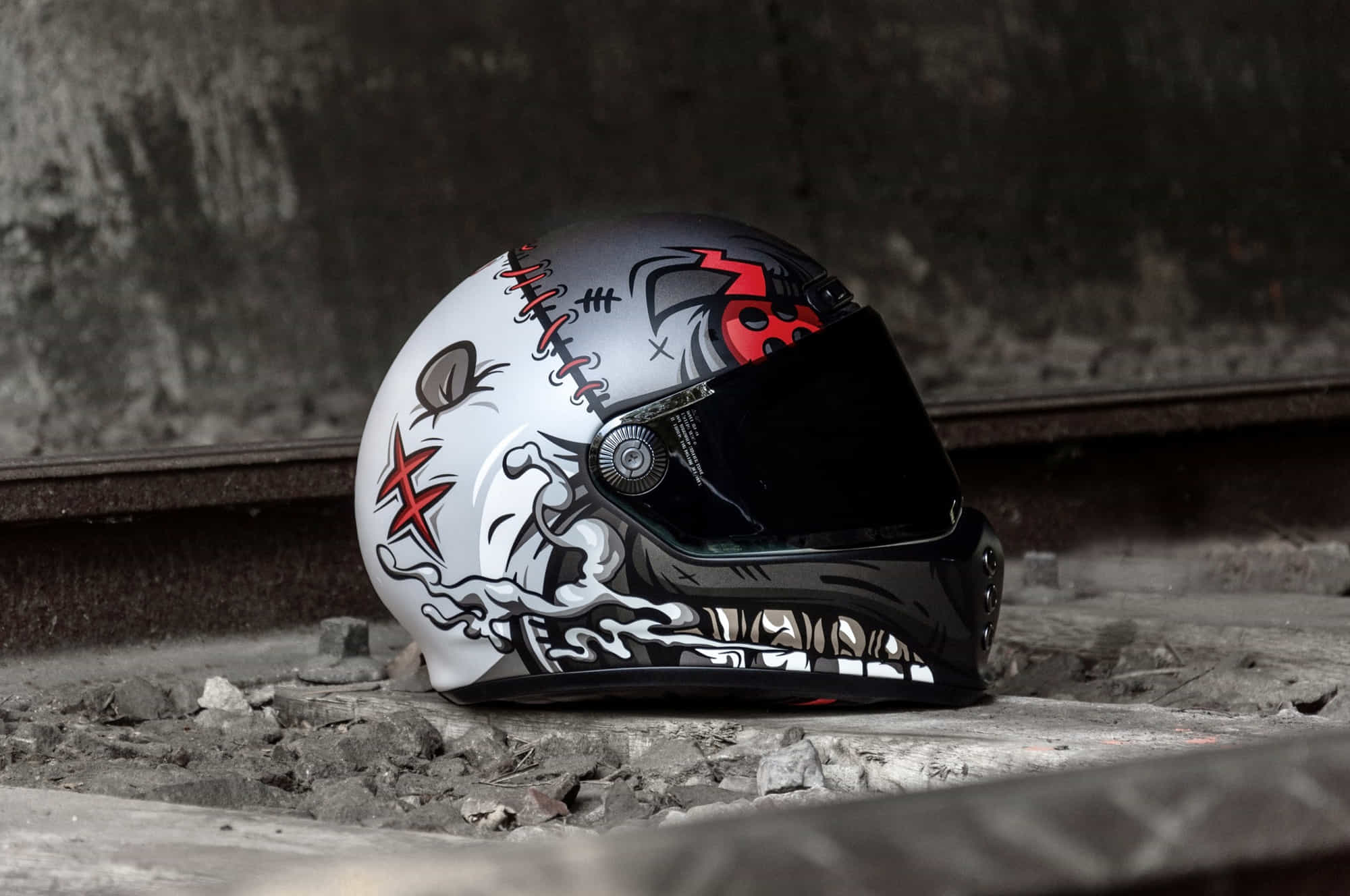